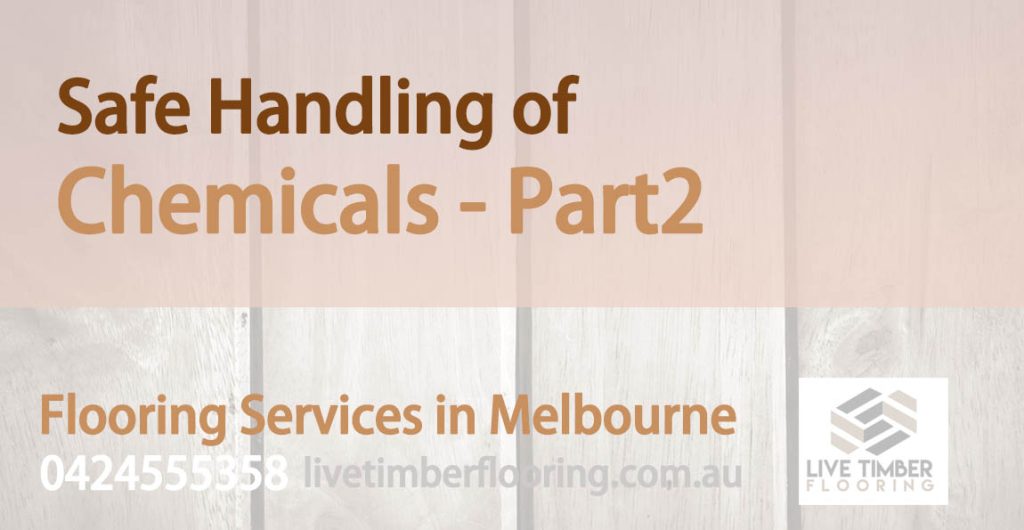
Solvent (oil) based finishes are the most commonly used sealer type in the industry. They dry fast and are easy to work and have been proven to give the best result. As an advantage, they provide a shiny floor that can withstand years of tear and wear. However, solvent-based products have flammable chemicals and absolutely a strong odour. The flash point of most oil-based sealers are bellow 200o F and thus, they are combustible. These finishes have adverse effects on human health as well as environment. Therefore, the use and storage of them have been restricted by law in many places. Please handle solvent based finishes with caution as they also disseminate strong fume and vapour, especially in cold winter day when windows are closed. If you are using these products, please be aware of potential danger and follow preventive measurement mentioned for Lacquer Sealers.
Water Based Finishes and Low VOC Oils
Since Water based floor finishes release only water, they are considered as safest hardwood finishing products. In fact, the best way to eliminate combustible floor products is by using water-based sealers. Although water-based finishes present zero fire hazard, like oil-based sealers, they include some chemicals which can be toxic or harmful. As proved by laboratory tests, the quality of non-flammable water-based products is better than almost any solvent-based product. The best is that they dry faster and the occupant can stay at home while the refinishing process is going on. The only drawback is that the appearance of the floor may not be as shiny and brilliant as oil-based sealers. However, an experienced hardwood professional can create the same look with water-based finishes utilizing some simple tricks.
Minimizing Inhalation of Vapour and Sawdust
Most hardwood finishing products contain organic solvent or other substances such as epoxies, urea-formaldehyde, polyurethane, and nitrocellulose resins and additives. Most of these chemicals are classified as Volatile organic compounds (VOCs). It means that they evaporate in normal room temperature and quickly fill the room. Prolonged and repeated exposure to vapours in hardwood refinishing products may cause both acute and chronic health problems such as to dizziness, eye, nose and throat irritation, headaches and damage to liver, kidneys and the central nervous system. In addition, some products that include benzene and formaldehyde, are suspected or known carcinogens. Formaldehyde is emanated from some floor adhesives or low-quality vinyl floorings. One way to get rid of the danger of VOCs in floor adhesives is installing the timber floor by nail or staple. Sanding a wooden floor will release tiny particle in the air that has been known as a source of cancer in human. Sanding a floor coated with lead or lead-based paints will also disseminate respirable lead particles. To minimize inhalation of harmful vapor and dust during hardwood sanding and finishing process, you should provide adequate venation to the room. It is recommended that the room is ventilated by natural or forced methods to ensure a dilution rate of at least 25% of the Lower Explosion Limit (LEL) of the solvent vapour mixture in the air. Don’t forget to wear a high-quality dust mask or respirator during the sand work or refinishing. It is better to get the sanding job done by companies equipped with dust collection systems for floor sanding.
Avoiding Direct Skin Contact
Some chemicals in surface finishing products can cause skin dermatitis and/or sensitization through direct skin contact. If toxic enough substances absorbed from the skin into the blood they may lead to adverse health effects. Hence, it is imperative to always wear protective gloves or use protective power when you deal with hardwood adhesives, sealers, and finishes. Chemical used in sanding and finishing jobs can cause health problem for both families and professionals if not handles properly. However, the risk can be managed by changing to safer products and following safety instructions. We have provided a list of chemical hazards in sanding and flooring and how to avoid them. To see the resources of this article, go to this page